With regard to
What is the main function of hot runner shunt plate manufacturing? The diverter plate is a part of diverting the molten material, which can transfer the molten plastic from the injection molding machine to the mold cavity, and its role is to transfer the molten raw material to the injection port, and in the case of friction and shear force and heating, as far as possible without changing the state of the molten material flow.
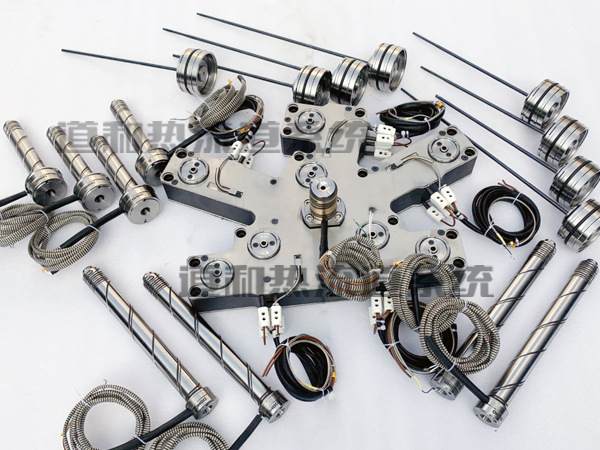
Most suppliers manufacture the diverter plate by drilling holes into the steel plate that has been initially contoured, and then install the heater on the steel plate or inside the steel plate. In most applications, the shunt plate design has several heating zones that are individually controlled by the thermostat.
There are many types of shunt plates, such as X type, H type, I type, Y type, K type, and others. According to the different heating methods of the hot runner, different product types can be selected.
There are two heating methods for the hot runner shunt plate, one is internal heating, that is, heating rods are set in the runner to heat plastics from the inside of the runner, and the other is external heating, generally opening heating holes in the direction parallel to the runner, inserting heating rods to heat the runner from the outside of the runner.
These two different heating methods have their own advantages, compared with the internal heating method, the thermal efficiency is higher, but the disadvantages are also more obvious, easy to cause local overheating in the hot runner system, and increase the flow resistance of the melt. The heating efficiency of the external heating method is relatively low, but the flow path is easy to process, the heating device is easy to buy, and the maintenance is convenient, but the heating efficiency is low.
In order to obtain the best results, the shunt plate design process should include a detailed injection molding product application analysis, such as product quality, raw material type and process expectations. The design of the shunt plate will affect the quality and function of the injection molded product.
In the unqualified shunt plate design, such as the molten material in the shunt plate to each nozzle flow length is different, will lead to an imbalance between the mold cavity, resulting in different product sizes, if not properly treated, the heat and shear process in the shunt plate will lead to polymer degradation, resulting in product performance defects and fading.